FRONT AXLECASTER ANGLEFig. 4 Toe-In MeasurementTURNING ANGLEFig. 5 Inner Wheel Turns in a Smaller Circle Than Outside WheelTROUBLE SHOOTINGTROUBLE SHOOTING - ContinuedFRONT AXLE - I-BEAM TYPESPECIFICATIONSSTEERING KNUCKLE BUSHINGSSteering Knuckle RemovalSteering knuckle Bushings (Nylon and Teflon)Steering Knuckle Bushing Installation (Bronze)KNUCKLE PIN INSTALLATIONTIE ROD ENDSDRAG LINKTORQUE CHARTREAR AXLESPECIFICATIONSSTD and STDD SERIESINTER-AXLE DIFFERNTIALDOUBLE REDUCTION DRIVE UNIT DESCRIPTIONREMOVE AND DISASSEMBLE DRIVE UNITREMOVE DRIVE UNIT FROM HOUSINGDISASSEMBLE INTERAXLE (3rd) DIFFERENTIAL ASSEMBLYREMOVE AND DISASSEMBLE HYPOID PINION AND QUILL, BEARING AND HOUSING ASSEMBLYREMOVE AND DISASSEMBLE HYPOID PINION AND QUILL, BEARING AND HOUSING ASSEMBLY - ContinuedREMOVE AND DISASSEMBLE THRUSHAFT ASSEMBLYREMOVE AND DISASSEMBLE THRUSHAFT ASSEMBLY - ContinuedREMOVE AND DISASSEMBLE THRUSHAFT ASSEMBLY - ContinuedCORROSION PREVENTIONREASSEMBLE AND INSTALL DRIVE UNITREASSEMBLE CROSS SHAFT ASSEMBLYREASSEMBLE CROSS SHAFT ASSEMBLY - ContinuedREASSEMBLE AND INSTALL HYPOID PINION AND QUILL, BEARING AND HOUSING ASSEMBLYASSEMBLE AND INSTALL THRU-SHAFT ASSEMBLYASSEMBLE INTERAXLE DIFFERENTIALSHIFT SHAFT ADJUSTMENTCORRECT TOOTH CONTACT ASSURES LONGER GEAR LIFEASSEMBLE AND INSTALL AXLE DIFFERENTIALINSTALLATION OF BEARING CUPS IN CARRIER LEG BORESCOMPLETE DRIVE UNIT ASSEMBLYHOW TO MATCH TANDEM TIRESTABULATION OF TORQUE LIMITSLOCKING TYPE DIFFERENTIALFig. 1 Internal Spring Design Differential Locking Unit (Exploded ViewFig. 3 Typical installation of No Spin, unit (Cross Sectional View)Fig. 4 Straight Forward DrivingFig. 8 Forward Left Hand Turn (Cross Sectional View)Fig. 10 Inserting Assembly Retaining BoltIMPORTANT PRECAUTIONFig . 12 Cutaway View of Tandem Lock NoSPIN Inter-Axle DifferentialFAILURE ANALYSISFAILURE ANALYSIS - ContinuedFig . 1-Scored and Scuffed Gear Teeth .Fig . 2-Scuffed Gear Teeth--Coast Sides Only .Fig . 3-Fractured Gear TeethFig. 4-Pitted Bevel Pinion TeethFig . 5-Fatigue Fracture-Bevel Drive PinionFig . 6-Overheated Gear Set .Fig . 7-Pitted Planetary Gear Teeth .Fig. 8-Shock Fracture.Fig. 9-Worn High Speed Clutch Plate and Differential Bearing AdjusterFig. 10-Worn Support Case Hub.Fig. 11-Scoring and Seizure of Spider and PinionsFig. 12-Fatigue Fracture-Differential Side GearsFig. 13-Fatigue Fracture-Misalignment.Fig. 14-Shock FractureFig. 15-Fatigue-At Axle Shaft FlangeFig. 16-Twisted ShaftFig. 17-Bent HousingFig. 18-Wear--Inner Bearing Bore.Fig. 19-Roller Bearing End Wear.Fig. 20 - Ball Inner Race Damaged From Circulation of Abrasive Material.Fig. 22 - Ball Bearing Inner Race Marked From False Brinelling.Fig. 24-Bearing Shield Damaged From Removal With Punch.Fig. 26 - Failure of Ball Separator As Result of MisalignmentBODIES AND CABS CONVENTIONAL RIVETED CAB INDEXFig. 1. Instrument Panel Gauges and ControlsFig. 2. Cab Assembly (Exploded View)Fig. 2. Cab Assembly (Exploded View) - ContinuedFig. 3. Cab Door Window and Vent Assembly (Exploded View)BODIES AND CABSWINDOW REGULATORVENT WINDOWCAB DOOR LOCK AND REMOTE CONTROLSUN VISORSUN VISOR - ContinuedCAB REAR WINDOW GLASSCAB REAR WINDOW GLASS INSTALLATIONWINDSHIELD WIPER MOTORFig. 41 Cab Mounting (Exploded View)Legend for Fig. 42Fig. 42. Cab Structure SectionsFig. 43 Cab Floor SubstructureBODY MOUNTINGSLUBRICATIONFig . 48. Exploded View of Front End Sheet Metal LegRadiator Sheet Metal ShellPROCEDURES AND INSTRUCTIONS FOR WELDING ALUMINUM CABS, BODIES AND STRUCTURESFig. 2. Diagram Showing Details of Shorting Arc Process and the Inert Gas ShieldingTYPICAL SHORTING ARC WELDING CONDITIONSFig. 3. Chipping Along Length of Crack. Chipping is not necessary on Sheet Aluminum.Crack RepairFig. 6. Showing method of applying short run of weld.PREPARATION OF ALUMINUM FOR PAINTINGFig. 10. Details of the plug weld.PROPERTIES OF ALUMINUMWELDING TERMSWELDING TERMS - ContinuedWELDING TERMS - ContinuedFIBERGLASS REPAIR INSTRUCTIONSFig. 1. Fiberglass Repair KitREPAIRING FIBERGLASSSmall Scratches or Chipped AreaFig . 1. "Air Viking" Suspension SeatAIR SUSPENSION SYSTEMFig. 7. Air Suspension SystemFig. 9. Shock Absorber RemovalFig. 10. Exploded View of Air Suspension SeatBENDIX WESTINGHOUSESPECIFICATIONSFig . 1 Exterior View of TuFlo 400 and 5 CompressorFig. 4 Compression of AirRemoving and Disassembling Cylinder HeadINSPECTION OF PARTSFig. 7 Measuring Piston DiameterFig . 9 Sectional View of Block and CrankcaseFig. 10 Installing Wrist Pin Lock WireFig. 13 Exploded View of Air StrainerTROUBLE SHOOTINGAIR BRAKE COMPONENTSAIR BRAKE COMPONENTS - ContinuedFig. 1 - Leak Detector Tester (SE2326)Fig . 2 Sectional View of type d-2 GovernorLeakage TestsASSEMBLY, ADJUST AND TESTCHAPTER II. RESERVOIR DRAIN COCK SAFETY VALVE PRESSURE GAUGE - LOW PRESSURE INDICATOR - STOP LIGHT SWITCHSERVICE CHECKSFig 5. Cross Sectional View of Low Pressure IndicatorFig 6. Stop Light SwitchAUTOMATIC RESERVOIR DRAIN VALVESERVICE CHECKSFig. 13 Sectional View of Automatic Reservoir Drain ValueASSEMBLYFig. 1 Cross Sectional View of One-Way Check ValveBRAKE VALVEInspection and CleaningFig. 1. Quick Release ValveFig. 2. Sectional View of Quick Release valveFig. 3 Limiting and Quick Release Valve CombinationSERVICE CHECKSRELAY VALVECLEANING AND INSPECTIONSPRING BRAKE AND TWO-WAY CONTROL VALVETWO-WAY CONTROL VALVEFig. 4. Sectional View of Type PB Two-Way Control ValveSERVICE CHECKSCLEANING AND INSPECTIONFLEXIBLE HOSE, NYLON TUBING, RIGID PIPING AND FITTINGSHose Assembly Special InstructionsFig. 6. Nylon Tubing assembly with Long nutSERVICE CHECKSALCOHOL EVAPORATORFig. 3. Cutaway View of AE-1 Alcohol EvaporatorTESTING FOR SERVICEABILITYTROUBLE SHOOTING GUIDETROUBLE SHOOTING GUIDE - ContinuedFig. 1. AD-1 Air DryerFig. 5. AD-2 Operational Charge CycleFig. 6. Operational Purge CycleREMOVAL OF DESICCANT CARTRIDGE AD-1 & AD-2Fig. 8. Installing O-RingsFig. 10 Installing Felt Cloth in CartridgeFig 14 Installing Second Perforated PlateREBUILDING AD-1 END COVER ASSEMBLYFig. 19 Purge Valve Assembly DisassembledOUTLET PORT CHECK VALVE ON AD-2FOUNDATION BRAKE - AIR CAM-ACTUATED TYPEFig. 1 Foundation Brake AssemblyFig. 2 Exploded View of Front Brake GroupFig. 4 Exploded View of Rear Brake GroupFig. 7 Brake Chamber and Slack AdjusterFig. 10 Scored Brake DrumFig. 13 Lining Selected Too ThickFig. 15 Sequence in Securing Brake Block Lining to ShoeFig. 19 Typical "Spring Brake" Air ChamberSLACK ADJUSTERSFig. 20 Sectional View of Slack AdjusterLUBRICATIONWEDGE ACTUATED TYPE - STOPMASTERINDEXSTOPMASTER BRAKESSTOPMASTER ACTUATING SYSTEMBRAKE ADJUSTMENTPOWER UNIT ADJUSTMENTSERVICE RECOMMENDATIONSTROUBLE SHOOTING GUIDERDA Bolted on Spider Mounted Integral Plunger HousingsSERVICING POWER UNITSREMOVING POWER UNIT FROM BRAKE ASSEMBLY.AIR CHAMBERSINSTALLING POWER UNIT ONTO BRAKE ASSEMBLYINSTALLING BOTTOMING TYPE POWER UNITSERVICING BRAKE SHOESASSEMBLE SEALS ONTO PLUNGERSINSTALL PLUNGERS INTO PLUNGER HOUSINGAUTOMATIC ADJUSTING PLUNGERSAUTOMATIC ADJUSTING PLUNGERS - ContinuedStopmater Brakes - Problem Analysis GuideMaintenance GuideRDA STOPMASTERSTOPMASTER II WEDGE BRAKE DESIGN IMPROVEMENTSADJUSTING PAWL ASSEMBLYGROOVED BRAKE LININGTROUBLE SHOOTING GUIDEREMOVE POWER UNIT FROM BRAKE ASSEMBLYREASSEMBLE AIR CHAMBERREMOVE AND DISASSEMBLE AUTOMATIC ADJUSTING ASSEMBLYPREPARE FOR REASSEMBLYTRUCK SERVICE MANUALSPRING ACTUATED-TANDEM TYPE 30 INCH CHAMBERSFig. 3 Type 30 Chamber.Fig. 4 Parking Brake and Service Brake in Released Position (Air Pressure Applied to Parking Brake Spring).Fig. 8 Backing Off Release Bolt.Fig. 9 Removing Clamp Ring.Fig. 13 Removing Head, Spring and Piston AssemblyFig. 17 Piston, Spring and Head Assembly.Fig. 19 Aligning Piston with Head Bore.Fig. 20 Early Model Parking Spring Brake Unit Having Mounting Plate and Rubber PadCOOLING SYSTEMANTIFREEZE - PERMANENT TYPEFig. 1 Radiator Cap (Pressure Type)Fig. 3 Installing Core Plug Using SE1725 Installer Tool with SE1581B Handle.Transmission Oil Cooler or Heat ExchangerPressure FlushingTest EquipmentTROUBLE SHOOTINGAUTOMATIC RADIATOR SHUTTERFig. 1 Radiator Shutter Control.Fig. 2 Radiator Control Assembly (Exploded View).Fig. 4 Shutter Control Thermostat Unit Adjustment.TROUBLE SHOOTINGTROUBLE SHOOTING (Continued)ALTERNATOR MODEL 27SI TYPE 200 80 AMPDESCRIPTIONUndercharged BatteryOvercharged BatteryRotor Field Winding ChecksRectifier Bridge CheckBearing Replacement and LubricationFig. 12 Connections for Bench Check of AlternatorTRUCK SERVICE MANUALELECTRICALFig. 1 Six-Volt Storage Battery (Cutaway)Fig. 6 Typical Multiple Battery InstallationFig. 7 Battery Maintenance ChecksFig. 9 Proper Jumper Cable ConnectionFig. 11 High Rate Discharge TesterPutting Dry Charged Batteries into ServiceFig. 14 Using Terminal PullerFig. 17 Spreading Cable Clamp with Terminal SpreaderPROPERTIES OF ELECTROLYTEBATTERY STOCK MAINTENANCECIRCUIT DIAGRAM AND CIRCUIT COMPONENTSCIRCUIT DIAGRAM AND CIRCUIT COMPONENTS - ContinuedFUSE AND CIRCUIT BREAKER PANELSFUSE PANEL AND CIRCUIT BREAKER PANEL LOCATIONSHEADLIGHTS SINGLEHEADLIGHTS SINGLE - ELECTRICALHEADLIGHTS SINGLE - ELECTRICAL - ContinuedHEADLIGHT AIMINGSTARTING MOTOR ENCLOSED SHIFT LEVER TYPEFig. 1 Heavy Duty Starting Motor with Enclosed Shift Lever.Fig. 3 Sectional View of Staring Motor with Heavy Duty Sprag ClutchFig. 5 Cranking Voltage TestFig. 7 Cranking Circuit TestFig. 8 Control Circuit TestINSPECTION AND REPAIRFig. 12 Testing Armature for GroundsPINION CLEARANCEFig. 15 Pinion Drive Clearance Check HookupMODEL NTC 290 CUBIC INCH DISPLACEMENT 855Fig. 2-1 Checking lubricating oil filler tube capMaintenance ScheduleCheck Oil Bath Cleaner Oil LevelFig. 2-4, (N10098) Lubricating oil filter (center bolt)Fig. 2-22, (N20311) Crankcase breather combination TypeFig. 2-27, (Ni1977) Checking belt tensionFig. 2-29, (N11974) Water pump -with idlerFig. 2-50, (Nl14230) Accessory drive pulley markingsFig. 2-52, (N114220) Valve set timing marksTable 2-14: Injector Adjustment (Oil Temperature)Fig. 2-63, (N10146) Vibration damper alignment marksChange Aneroid Oil And Replace BreatherReplace Bellows And Calibrate AneroidSEASONAL CHECKSFig. 2-70, (N11953) Tightening turbocharger mounting nutsTable 2-18: Thermal Control SettingsTable 3-3: Arctic Oil RecommendationsTable 3-4: Spin-On Type DCA Water FilterTrouble ShootingTrouble Shooting - ContinuedTrouble Shooting - ContinuedOperating PrinciplesFig 5-1, (FWC-13) Fuel flow diagram - PT (type G) pump- inline engineFig. 5-7, (F5244). Aneroid cutawayFig. 5-11, (FWC 29),. Fuel injection cycle PT (type D) injector 5/16 inch diameter plunger.Cooling SystemINDEX855 CUBIC INCH DISPLACEMENT855 CUBIC INCH DISPLACEMENT - ContinuedIntroductionTRUCK SERVICE MANUAL - ENGINEEngine Disassembly Group 0Fig. 0-4, (N100120). Removing fan hub assembly (FFC Series)Fig . 09, (N 10093) .Removing vibration damper - Viscous typeConnecting Rod And Piston AssembliesSteam CleaningFig . 10 . Cylinder block, exploded viewTable 1-1: Cylinder Block Specifications - Inch [mm] (Reference Fig. 1-0)Table 1-1: Cylinder Block Specifications - Inch [mm] (Reference Fig. 1-0) (Cont.)Table 1-1: Cylinder Block Specifications - Inch [mm] (Reference Fig. 1-0) (Cont.)Table 1-1: Cylinder Block Specifications - Inch [mm] (Reference Fig. 1-0) (Cont.)CYLINDER BLOCKFig. 1-1 (N 10103). Cylinder liner counterbore dimension locationFig. 1-2 (N10181) Cylinder block height check location.Cylinder Head Capscrew ThreadsCLEAN DRILLINGS IN CRANKSHAFTFig . 143 (V50138) Identification of rod and main journal sizeFig. 1-6 (V40114). Connecting rod specifications.Fig. 1-8 (N10194) . Connecting rod wear limitsFig. 1-10. (N10158) Installing piston pin bushing in rod.Chamber Piston Pin BoreFig. 1-11 (N20171) Piston check points.Fig. 1-12. (N10145). Gear case cover and trunion bushing.Fig. 1-13, (V40156). ST-1059 Counterbore ToolINSTALLATION AND OPERATIONMACHINING THE BLOCKFig. 1-15, (V40172). ST-1168 Boring Tool.Fig. 1-16, (ST-1177). Exploded view of ST-1177 Boring ToolASSEMBLING MICROMETER TOOL BIT SETTING GAUGE AND TOOL BITUSE OF THE BRIDGESFig . 2-1 (N10295) . Cylinder head - exploded viewTable 2-1: Specifications - Inch [mm] (Reference Fig . 2-1)Table 2-1: Specifications - Inch [mm] (Reference Fig. 2-1) (Cont.)Fig. 2-2 (N10278) ST-1179 Injector sleeve holding toolFig. 2-4 (N10228) Valve seat insert-cross sectionValve Crosshead Guides And CrossheadsFig. 2-7 (N10231) Minimum valve head rim thicknessResurface Cylinder HeadSleeve InstallationGrind ValvesINSTRUCTIONS FOR USE OF SERVICE TOOLSST-1010 Water Hole Counterboring ToolFig. 3-1. (N1039). Rocker levers, shaft and housingFig. 3-2, (N 10318). Breather hole locationFig. 3-4, (N10326). Rocker lever assemblyROCKER HOUSING COVERFig. 4-1, (N10419). Cam followers and push tubesFig. 4-2 (N10412) Cam follower exploded viewPUSH TUBESFuel SystemFig. 7-0 Lubricating oil pump, exploded viewTable 7-5: Lubricating Oil Pump Specifications - Inch [mm) (Reference Fig. 7-0)Table 7-5: Lubricating Oil Pump Specifications - Inch [mm) (Reference Fig. 7-0) (Cont)LUBRICATING OIL DIPSTICKFig. 7-1. (V40726) Dipstick markingsFig. 7-3 (V50709) By-pass filter installationFig. 7-8 (N10705) Aligning oil cooler index marksFig. 7-9 (N10741) Lubricating oil cooler exploded viewREPAIR (HEADER LEAKS)ASSEMBLYFig. 8-1, (N10843). Water pump exploded view (855 C.I.D Series)WATER PUMP/I D LER (FFC SERIES-ECCENTRIC)THERMOSTAT AND HOUSINGFig. 8-4, (N 10839). Fan hub assembly with tapered roller bearing and spacerTable 9-1: Drive Unit Specifications - Inch [mm]Fig. 9-1, (N10903). Fuel pump or compressor driveFig. 9-2, (N10906). Fuel pump, hydraulic governor and hourmeter driveDRIVE PULLEYS INSPECTION AND REPAIRFig. 10-1, (N21019). Glow plug preheater adapter spray nozzleFig. 10-2, (CGS-20). Air cleaner restriction indicatorTURBOCHARGERSFig. 14-1, (N 1142356). Engine exploded viewCrankshaft Flange Capscrew Torque Specifications - ft-lb. [kg m]Crankshaft And Main BearingsCylinder LinersFig. 14-4, (N11424). Checking gear backlashFig. 146, (N114236). Cam follower torquing sequenceFig. 148, (Ni1432). injection timing procedureFig. 14-9, (N11463). Rocker lever housing torquing sequenceFig. 14-11, (N114129). Checking lubricating oil pump gear backlashFig. 14-12, (N114134). Checking gear case cover to block alignmentFig. 14-15, (N11448). Indicating flywheel housing faceFig. 14-16, (N114136). Checking oil pan to block alignmentFig. 14-21, (N114140). Checking vibration damper run-outFan Hub And PulleyWater Manifold And Thermostat HousingFig. 14-24, (N11471). Checking belt tension manuallyFig. 14-25, (N114220). Valve set timing markFig. 14-28 (N114237), Bottoming Injector plunger in cupFig. 14-30, (N1 1466). Adjusting injector plungerFig. 14-31, (N114215). Adjusting valvesFig. 1433, (N11963). Lubricating system priming pointCold Start With PreheaterCHECKS DURING RUNING TESTTable 1415: Normal Lubricating Oil PressureANEROID CONTROL ADJUSTMENTTemporary StorageInspectionWATER TEMPERATURE GAUGEFig. 15-1 (VI1306). Wiring diagramFig. 16-1A (V11306A). Wiring diagram (cont'd.)Fig. 15-18 (V11306B). Wiring diagram (cont'd.)Specifications and Wear Limits Group 18Specifications and Wear Limits Group 18 - ContinuedSpecifications and Wear Limits Group 18 - ContinuedSpecifications and Wear Limits Group 18 - ContinuedSpecifications and Wear Limits Group 18 - ContinuedSpecifications and Wear Limits Group 18 - ContinuedSpecifications and Wear Limits Group 18 - ContinuedSpecifications and Wear Limits Group 18 - ContinuedCAPSCREW MARKINGS AND TORQUE VALUESTable 18-1: Oil RecommendationsTable 18-2: Operating Temperatures Vs ViscosityRecommended Fuel Oil PropertiesTable 18-5: Package or Canister D C A Water FilterFig. 20-2. (N12045 J). Clearance area between lever and crossheadFig. 20-5. (N12032 J). Wiring diagramIndexIndex - ContinuedIndex - ContinuedIndex - ContinuedIndex - ContinuedIndex - ContinuedIndex - ContinuedIndex - ContinuedIndex - ContinuedIndex - ContinuedGENERALREPAIR AND REINFORCEMENTSFig. 5 Suggested Types of Reinforcing Plates and Method of Attaching to Frame Rail.REPAIR AND REINFORCEMENTSREPAIR AND REINFORCEMENTS - ContinuedFrame StraighteningAIR CLEANER INDEXFig. 1 Dry Type Air CleanerFig. 2 Heavy Duty Dry Type Air CleanerInjectors PT typeFig. 6-1-5, FWC27. Cylindrical PT (D) injector cross-sectionFig. 6-1-9, F60197. Loosening cup retainerFig. 6-1-17, F60105. New injector cup tipFig. 6-1-20, F60108. Seat pattern of plunger In cupFig. 6-1-32, F60194. Installing cup on barrelFig. 6-1-38, F60198. Checking plunger to cup bindingFig. 6-1-40, F60200. Size location on Injector adapterFig. 6-1-44, F60167. ST990 injector leakage testerFig. 6-1-46, F60169. Bubble check or bowl oil levelFig. -1-56, F6234. Inserting injector into ST-1058 potFig. 6-1-62, F60176. Rotating plunger coupling and spacerFig. 6-1-36, F60207. PT (type D) Injector in ST668Table 6-1-14: ST-668 Cup Seat SpacerFig. 6-1-70, F60124. Clamping cylinder and seatFig. 6-1-75, F60129. Measuring fuel in vialFig, 6-1-77A, F60160. Clutch arm removal and clutch adjustmentFig. 6-1-79, F60182. Filling gauge to remove air bubblesFig. 6-1-81, F60131. ST789 load cellFig. 6-1-85, F60135. Position assemblyFig. 6-1-88, F60138. Start counter at zeroFig. 6-1-92, F60142. Installing restrictor orificeFig. 6-1-109, F60203. Center injector inlet in ST1058 inlet holeFig. 6-1-111, F60213. Check leakage at inlet portFig. 6-1-114, F60216. Knob spacingFig. 6-1-94, F60143. Orifice size gaugeTrouble Shooting The ST790Complaints And CorrectionsFig. 6-1-121, Test stand hydraulic systemCHECK 4 FUEL GAUGEFig. 6-1-123, F60159. Hydraulic loading cylinderCheck 11 - Plunger Actuating LinkCheck 14 - Solenoid ValveCheck 2 - Test Oil TemperatureCheck 3 - Check Ball TravelCheck 1 - Filter InstallationCheck 2 - Defective Barrel To Adapter SealCheck 6 - Excessive Link WearFUEL PUMP - PT REBUILDINGFig. 1, F5295. PT (type G) AFC fuel pumpFig. 5.1, FWC-33. Fuel flow in PT fuel systemGear Pump And Pulsation DamperFront Drive Cover And Governor PlungerFUEL PUMP FILTER SCREENFig. 5-17, F514. Reaming drive shaft bushing with ST-490Fig, 5-23, F5139. Removing torque springFig. 5-24, F5301. Removing AFC side cover plateFig. 5-27, F5304. Removing AFC barrel retaining ring.Fig. 5-30, F5140. Tachometer and matching drive gearsFig. 5-33, F524. Locating notches for right hand pump.Fig. 5-36, F5132. Pulsation damper - exploded viewFig. 5-38, F528. Inspecting plate type valveFig. 5-44, F5232. High pressure fuel shut-down valve AssemblyFig. 5-48, F539. Removing snap ring from grooveFig. 5-53, F541. Pressing drive bearing on shaftFig. 5-57, F544. Securing snap ring in grooveFig. 5-68, F5148. Standard governor - exploded viewFig. 5-94, F556. Installing tachometer driveFig. 5-97, F558. Installing washer over idle screwFig. 5-103, F564. Installing throttle restriction plungerFig. 5-109, F562. Torquing gear pump capscrewsFig. 5-126, F-5187.ST-1162 fuel pump throttle adjustment templateINDEXFUEL PUMP PT (TYPE G) CALIBRATION INSTRUCTIONSFUEL PUMP PT (TYPE G) CALIBRATION INSTRUCTIONS - ContinuedFig. 5-1-1, F5100. Cummins ST-848 Fuel pump test standChemical And Physical RequirementsFig. 5-1-3, F5164. Cummins ST-445 Fuel pump test strandFig. 5-1-5, F5169. Mounting fuel pump with spline driveFig. 5-1-11, F5104. Shim throttle restriction plungerFig. 5-1-13, FWC-31. PT Type G) Fuel pump cross-section and flowFig. 5-1-18, F5240. Comparison of fuel pump springsFig. 5-1-20, F5112. Adjust throttle leakage rateFig, 5-1-24, F5239, Setting throttle travel with protractorFig, F-1-27, F5117. Check weight assist effectFig. 5127B, F5272. Spring pack cover plug removed, pump at 600 RPM.Throttle LeakageHousing Porosity CheckTable 5-1-9: Gear Pump FlowComplaint and CorrectionsComplaint and Corrections - ContinuedComplaint and Corrections - ContinuedComplaint and Corrections - ContinuedComplaint and Corrections - ContinuedFig 52 1, N 11026 Aneroid mounted on engineFig. 5-2-3, F5287. Adjusting aneroid fuel screwTable 5-2-3: Starting Check Valve Spring SpecificationsAir Actuation Pressure Setting Of Turbocharger EnginesFig. 5-2-7, F5249. Aneroid exploded viewMaintenance, Trouble Shooting And Repair MaintenanceAdjustment On EngineChecking and Adjusting Fuel Manifold PressureFig. 531, F5178. Checking fuel manifold pressureEngine PowerFig. 535 F5181. Sealing fuel pumpFig. 5 3 6. F5241. Drilling spring pack housing with ST1175TURBOCHARGERVT-50 TurbochargersOperation and MaintenanceFig. 104, TA2. Checking air inlet restrictionMajor Cleaning OperationTrouble ShootingTrouble Shooting - ContinuedTrouble Shooting - ContinuedFig. 10-8, T-516. Pulling impeller from rotor shaftFig. 10.9, T-418. Removing oil seal diffuser plateFig. 10-15, T-31 1. Inspecting turbine casingFig. 10-18, T-431. Checking rotor thrust surfaceFig. 10-20, T-316. Measuring floating bearing O.D.Fig. 10-28, T-536. Installing "O" ring on bearing housingFig. 10-24, T-433. Installing sealing ringFig. 10-36, T-421. Torquing "V" clamp bolts and nutsFig. 10-38, T-545. Checking rotor end clearanceFig. 10-40, T-333. Turbocharger mountingVT-50 SpecificationsINSTRUMENT GROUPFig. 1. Electrical Instrument Gauge Printed Circuit BoardSPEEDOMETERFig. 17. Semi-Rigid Speedometer Cable.AC MANUFACTURED INSTRUMENT GAUGESFig. 21. Battery-Generating System Indicator GaugeFig. 22. Fuel Gauge CircuitFig. 24. Checking Fuel Level Gauge System ComponentsFig. 25. Checking Fuel Level Gauge System ComponentsFig. 27. Oil Temperature Gauge CircuitOil Temperature GaugeLUBRICATION FOR LUBRICATION INTERVALS REFER TO OPERATORS MANUALAXLE - REARBRAKES (Continued)ELECTRICAL ENGINE ENGINE (Continued)POWER TAKE OFFSTEERING TRANSMISSION WHEEL BEARINGSPROPELLER SHAFTFig. 1 Typical Propeller Shaft InstallationFig. 3. "Broken Back" Type Drive LineFig. 4. Universal Joint Speed FluctuationsFig. 6. Slip Joint Alignment ArrowsFig. 7. Balancing Parking Brake DrumFig. 9. Drive Line Horizontal and Vertical AlignmentFig. 11. Measuring Mounted Engine AngleFig. 12. Checking Main Transmission Companion Flange Vertical AlignmentFig. 14. Main and Auxiliary Transmission Center Lines Not ParallelFig. 16 Rear Axle Pinion Shaft and Engine Crankshaft Horizontal Center Lines ParallelFig. 18 Checking Yokes for DistortionFig. 19 Checking Yoke Run-OutTROUBLESHOOTINGUNIVERSAL JOINTSDISASSEMBLY - SOLID CROSS TYPEREASSEMBLY SOLID CROSS TYPESPRINGSFig. 7 Lubricated Spring Shackle (Driven-in type spring pin).Cleaning, Inspection and RepairTROUBLESHOOTINGEQUALIZING BEAM SUSPENSIONSUSPENSION SYSTEM TORQUE CHART (NEWTON METERS)Fig. 1. Tandem Axle with Equalizing Beam SuspensionLUBRICATIONREPLACING EQUALIZER BEAM BUSHINGSFig. 9 Installing Equalizer Beam End BushingFig. 11 Installing Center Sleeve and BushingFig. 13 Exploded View of Leaf Spring Type SuspensionInstalling Equalizer Beams and Cross TubeInstalling Axle AssembliesADAPTER CHARTPOWER STEERING PUMPSPECIFICATIONSIdentification of Numbers and LettersFig. 1. Cutaway of Pump.DISASSEMBLYFig. 5 Exploded View of Pump.DISASSEMBLY - ContinuedDISASSEMBLY - ContinuedREASSEMBLYTROUBLESHOOTING PROCEDUREFig. 19 Pressure Gauge Installed in SystemPRESSURE CHECKING THE POWER STEERING PUMP SYSTEMSTEERING GEAR WITH INTEGRAL POWERSPECIFICATIONSFig. 1 External ViewFig. 5 Pitman Arm PullerDISASSEMBLYDISASSEMBLY - ContinuedDISASSEMBLY - ContinuedDISASSEMBLY - ContinuedCLEANING, INSPECTION AND REPAIRCLEANING, INSPECTION AND REPAIR - ContinuedCLEANING, INSPECTION AND REPAIR - ContinuedBleeding Air from SystemADJUSTING RELIEF VALVE PLUNGERSSchematic of Dual Integral Power Steering Gear SystemSecondary GearFig . 42 Exploded View of Steering Gear (Dual System)TROUBLE SHOOTING CHARTTROUBLE SHOOTING CHART - ContinuedTROUBLE SHOOTING CHART - ContinuedTORQUE CHARTSTEERING COLUMN ASSEMBLYFigure 1.Fig . 2 Plastic Horn Button RemovalFig . 3 Steering Wheel Removal Using Puller SE-1821Fig . 7 Remove Steering Jacket Tube Bearings Using Puller SE-1746Fig. 9 Bearing Removal, Yoke in ViseFig . 13 Snap Ring InstallationFig . 15 Steering Gear AlignmentTORQUE CHARTTORQUE CHART - ContinuedIMPORTANT SAFETY NOTICETABLE OF CONTENTSSection 3. PREVENT MAINTENANCESection 4. GENERAL OVERHAUL INFORMATIONSection 6. REBUILD OF SUBASSEMBLIESSection 7. ASSEMBLY OF TRANSMISSION FROM SUBASSEMBLIESSection 8. WEAR LIMITS AND SPRING DATAFOLDOUTSSection 1. GENERAL INFORMATIONFig. 1-4. Model HT 750 transmission-right-front viewFig. 1-7 Transmission name plateSPECIFICATIONS AND DATASPECIFICATIONS AND DATA CHARTSPECIFICATIONS AND DATA CHART - ContinuedGENERAL INFORMATIONSection 2. DESCRIPTION AND OPERATIONDESCRIPTION AND OPERATIONHT 700D SERIES TRANSMISSIONSDESCRIPTION AND OPERATIONHT 700D SERIES TRANSMISSIONSDESCRIPTION AND OPERATIONHT 700D SERIES TRANSMISSIONSDESCRIPTION AND OPERATIONHT 700D SERIES TRANSMISSIONSHT 700D SERIES TRANSMISSIONSClutch Circuit, Drive RangesHT 700D SERIES TRANSMISSIONSDESCRIPTION AND OPERATIONFig. 2-8. Neutral torque pathFig. 2-9. First-gearFig. 2-10. Second-gear torque pathFig. 2-11. Third-gear torque pathFig. 2-12. Fourth-gear torque pathFig. 2-13. Fifth-gear torque pathFig. 2-14. Reverse-gear torque pathSection 3. PREVENTIVE MAINTENANCEHT 700D SERIES TRANSMI SSIONSPREVENTIVE MAINTENANCEHT 700D SERIES TRANSMISSIONSPREVENTIVE MAINTENANCEEXTERNAL LINES AND OIL COOLERSHIFT POINT CHECKPRESERVATION AND STORAGEStorage, 1 Year-Without OilCHECKING OIL PRESSURESFig. 3-1. Transmission check points, external connections (c,/o retarder)Fig. 3-2 Oil pressure check points (with retarder)TROUBLESHOOTING CHARTTROUBLESHOOTING CHART - ContinuedTROUBLESHOOTING CHART - ContinuedTROUBLESHOOTING CHART - ContinuedSection 4. GENERAL OVERHAUL INFORMATIONFig., -1. Work tableSPECIAL TOOLS TABLE (fig. 4-2, 4-3, 4-4)Fig. 4-3 Special tools (24 through 55)Fig. 4-4 Special (56 through 60)CLEANING, INSPECTIONInspecting BearingsFig. 1-5 Method of measuring clutch plate coneTORQUE SPECIFICATIONSFig. 5-1. Installing transmission overhaul standFig. 5-3. Removing modulator actuator rodFig. 5-7. Removing oil pan screwsFig. 5-11. Removing oil filterFig. 5-16 Control valve body bolt locationsFig. 5-19 Removing torque converter pumpFig. 5-26 Removing torque converter housingFig. 5-31 Removing forward clutch assemblyFig. 5-37 Removing second-clutch snapringFig. 5-41 Removing rear coverFig. 5.44. Removing first clutch plates .DISASSEMBLYSection 6. INSPECTION AND REBUILD OF SUBASSEMBLIESFig. 6-5. Components of control valve assemblyFig. 6-6. Ball locations for control valve.Fig. 6-7. Control valve assembly - with components installed.LEGEND FOR FIGURE 6-7.HT 700D SERIES TRANSMISSIONSINSPECTION AND REBUILDFig. 6-8 Tightening selector valve stop bolt .Fig. 6-9. Installing stator freewheel rollerFig. 6.12. Torque converter pump components.Fig. 6.14. Supporting oil pump during removal.Fig. 6-15. Oil pump and torque converter housing .Fig. 6-17. Tool for installing front support needle bearingFig. 6-20 Checking oil pump drive gear end clearanceFig. 6-29 Forward clutch componentsFig. 6-31 Removing PTO gear from forward clutchFig. 6-35 Forward clutch assembly cross sectionFig. 6-36 Installing forward clutch pistonFig. 6-39 Removing (or installing) fourth clutch rear bearing raceFig. 6-12 Installing fourth clutch pistonFig. 6-4. Checking fourth clutch running clearanceFig. 6-17 Installing orifice plug into main shaftFig. 6-50 Removing output shaft rear oil sealFig. 6-52. Removing (or Installing) output shaftFig. 6-54. Removing speedometer driven gear bushingFig. 6-57. Installing piston into rear coverFig. 6-59. Installing output shaft bushingFig. 6-62. Installing manual shaft oil sealFig. 6-63. Components of low planetary carrier assemblyFig. 6.65. Removing retainer rings from first clutchFig. 6-66. Components of gear unit and main shaft assembly (HT750CRD)FLEX DISK ASSEMBLYFig. 6-68. Components of front planetary carrier assemblyCENTER PLANETARY CARRIER ASSEMBLYFig. 6.69 Components of center planetary carrier assemblyFig. 6-72. Components of rear planetary carrier assembly Fig. 6.74. Torque requirements for threaded fastenersFig. 7-4. Installing second clutch snapringFig. 7-6. Checking selective snapring clearanceFig. 7-9. Installing rear cover assemblyFig. 7-11. Checking first clutch clearanceFig. 7-12. Installing first clutch platesFig. 7-15. Installing second clutch plateFig. 7-17. Installing center supportFig. 7-19. Low planetary carrier, ring gear and clutchFig. 7-24. Installing center supportINSTALLING FOURTH, THIRD, FORWARD CLUTCHESFig. 7.33. Installing third clutch snapringFig. 7-35. Installing forward clutch assemblyFig. 7-38 insulating pilot tube screwFig. 7-47 Installing snapring onto the converter ground sleeveFig. 7.53 Installing control valve bodyFig. 7-56 Valve body assemblies (HT750)Fig. 7-58 Installing flywheel and turbineFig. 7-61 Installing modulator actuator rodFig. 7-63 Removing transmission from overhaul standPOWER TAKEOFF COMPONENTSSection 8. WEAR LIMITS AND SPRING DATAWEAR LIMITS AND SPRING DATAWEAR LIMITS AND SPRING DATA - ContinuedWEAR LIMITS AND SPRING DATA - ContinuedWEAR LIMITS AND SPRING DATA - ContinuedWEAR LIMITS AND SPRING DATA - ContinuedWEAR LIMITS AND SPRING DATA - ContinuedWEAR LIMITS AND SPRING DATA - ContinuedFoldout 2. Model HT 750CRD Transmission - Cross Section ViewLEGEND FOR B, FOLD OUT 7.B, foldout 7. Lockup clutch and torque converter-exploded viewA, foldout 7. Flex disc and flywheel assemblies-exploded viewB, foldout 10. Front support and valve assembly-exploded viewA, foldout 11. Forward clutch assembly-exploded viewB, foldout 11. Fourth-clutch assembly-exploded viewLEGEND A FOLDOUT 12A, foldout 12. Third-clutch, center support, and second clutch-exploded viewLEGEND FOR A, FOLDOUT 13A, foldout 13. Gear unit and main shaft assembly exploded viewLEGEND A, FOLDOUT 14A, foldout 14. Transmission housing, oil filter and oil pan-exploded viewB, foldout 14. First clutch--exploded viewA, foldout 15. Adapter housing, low-clutch plates and low carrierLEGEND A, FOR FOLDOUT 16A, foldout 16. First and low piston, rear cover, output shaft and governor-exploded viewLEGEND B, FOR FOLDOUT 16B, foldout 16. Control valve assembly-exploded viewA, foldout 17. Lockup cutoff, low shift and low trimnmer valve body assemblies-exploded viewINDEXSHIFT ROD ARRANGEMENTSSPICER TRANSMISSION LUBRICATIONAUXILIARY TRANSMISSION ASSEMBLYSHIFTER HOUSING FRONT CONTROLFigure 1INSTALLATION OF SHIFTER HOUSING ON CASEGEARS AND CASEMAINSHAFT REMOVAL & DISASSEMBLYFigure 5COUNTERSHAFT REASSEMBLY IMPORTANTMAINSHAFT ASSEMBLY AND INSTALLATION PARTIAL INSTALLATION OF MAIN DRIVE GEARMAINSHAFT ASSEMBLYINSTALLATION OF MAINSHAFTINSTALLATION OF MAINSHAFT - ContinuedINSTALLATION OF MAINSHAFT - ContinuedIMPORTANT PROCEDUREDriver TrainingWalking or Jumping Out of GearJumping Out of GearInterchangeabilityWHEELS, DRUMS, RIMS AND TIRESWHEELS, DRUMS, RIMS AND TIRES - ContinuedWHEEL BEARING ADJUSTMENTFig. 3 Heavy DutyFig. 4. Medium DutyUNITIZED OIL SEAL (AXLE RING NOT REQUIRED)Unitized Seal InstallationINITIAL LUBRICATION OF WHEEL BEARINGSBRAKE DRUMSBRAKE DRUMS - ContinuedFig. 2 Drop Center Type Disc Wheel (Tubeless)Wheel Studs and Mounting NutsRIM TIGHTENING AND ALIGNMENTWHEEL AND TIRE BALANCINGFig. 11 Chart Showing Effects of BleedingFig. 13 Speed vs. MileageThe next three steps apply only to the hot patch method.MOUNTING AND DISMOUNTING TIRESMOUNTING NUTS (Disc Wheels)ONE PIECE DROP CENTER HEAVY DUTY TUBELESS TIRES (7.00-20 and Up)Mounting InstructionsMounting Instructions - ContinuedTHREE-PIECE FLAT BASEMountingLOAD AND INFLATION CHARTTORQUE CHARTCONTENTSSINGLE SPEED - TWOMODEL NUMBER CONSTRUCTION 26DD SERIES EXTRA HEAVY DUTY P.T.O.Fig. 1. PTO Lubrication Adaptation'Unknown' by LOGSA - Page 881 of 894P.T.O COMMON PARTS LIST FOR 26DD SeriesGovernor DriveSERVICE INSTRUCTIONS FOR THE C10000 SERIES TELESCOPIC CYLINDERSSERVICE INSTRUCTIONS FOR THE C10000 SERIES TELESCOPIC CYLINDERS - ContinuedDIRECTIONAL CONTROL VALVEPUMP SERVICE REMOVALMarvel "12-IN-1" Hydraulic Filters for Suction, Return, and Low Pressure LinesSimplified OrderingDUMP BODY COMPONENTS
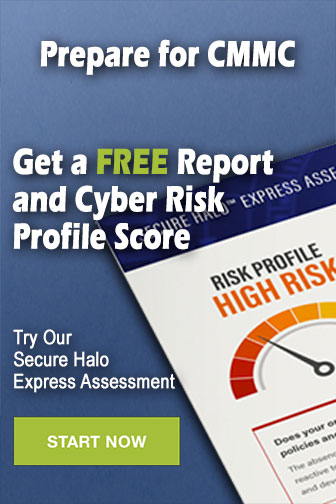