TM 5-3805-264-14&P
4-29.
EXPLANATION OF TABLE ENTRIES (Cont).
NOTE
The WARNINGS and CAUTIONS appearing in your PMCS table should always be
observed. WARNINGS and CAUTIONS appear before applicable procedures. These
WARNINGS and CAUTIONS must be observed to prevent serious injury to yourself
and others or to prevent your equipment from being damaged.
d.
Procedure Column. This column gives the procedure you must perform to check or service the
item listed in the Item to Check/Service column to know if the equipment is ready or available for its intended mis-
sion or for operation. You must perform the procedure at the time stated in the interval column.
e.
Not Fully Mission Capable If: Column. Information in this column tells you what fault will keep
your equipment from being capable of performing its primary mission. If you make check and service procedures
that show faults listed in this column the equipment is not mission-capable. Follow standard operating procedures
for maintaining the equipment or reporting equipment failure.
4-30.
GENERAL LUBRICATION PROCEDURES.
NOTE
Refer to Appendix J, Lubrication Instructions, for Lubrication Chart, key, localized
views, and procedural notes.
a.
Recommended intervals are based on normal conditions of operation, temperature, and humidity.
When operating under extreme conditions, lubricants should always be changed more frequently. When in doubt,
notify your supervisor.
b.
Keep all lubricants in a closed container and store in a clean. dry place away from extreme heat or
cold, Keep container covers clean and do not allow dust. dirt, or other foreign material to mix with lubricants. Keep
all lubrication equipment clean and ready for use.
c.
Maintain a good record of all lubrication performed and report any problems noted during lubrica-
tion, Refer to DA Pam 738-750 for maintenance forms and procedures to record and report any findings.
d.
Keep all external parts of equipment not requiring lubrication free of lubricants. Before lubrication,
wipe lubrication fittings with a clean rag (Item 15, Appendix F). After lubrication, wipe off excess oil or grease to
prevent accumulation of foreign matter.
e.
Refer to FM 9-207 for lubrication instructions in cold weather.
f.
Refer to AR 70-12 for use of standardized lubricants.
g.
Hydraulic oil filter element will be changed when:
(1)
it is known to be contaminated or clogged.
(2)
it is directed by Army Oil Analysis Program (AOAP) laboratory analysis.
h.
Hydraulic oil must be sampled initially at 90 days of operation, as prescribed by DA Pam 738-750.
Thereafter, it is sampled annually unless AOAP results dictate otherwise.
4-14
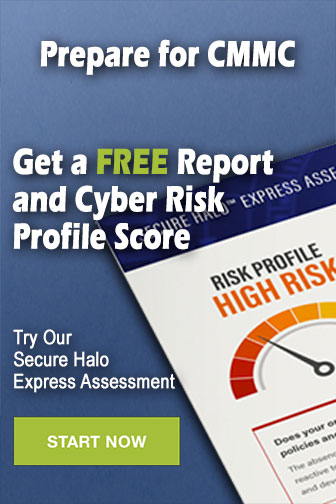